A new wave of tariffs is reshaping how American manufacturers think…
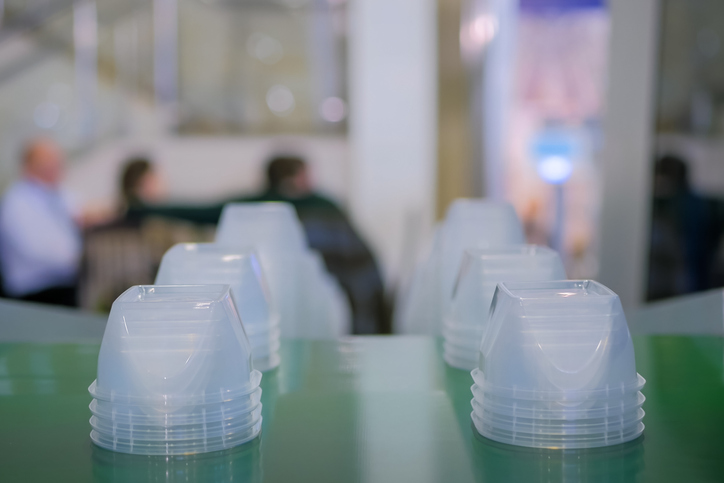
Saving Time and Money With Mold Flow Analysis
Plastic injection molding is a widely used process for producing parts. However, it is a complex process, and the product’s aesthetic and mechanical properties can be impacted by the process’s many variables, including the polymer’s properties, mold design, machine settings, and environmental conditions. If these are not all considered during the design phase, defects can occur.
The biggest investment you will make when manufacturing plastic injection molded parts is your tooling. It is critical that you get the part design and the mold correct before you start building it. It can be challenging for the most knowledgeable engineer to consider all the variables that may impact manufacturing a part, especially if it has a complex geometry or tight tolerances. Fortunately, a tool is available that assists with this. Our engineers use AutoDesk® Moldflow® simulation software to ensure your parts can be made efficiently and meet your quality requirements.
What is Mold Flow Analysis?
Mold flow analysis uses software to simulate the injection cycle and examine how a specific melted polymer will move through the mold based on desired parameters (temperature and pressure). It allows our engineers to test various molding conditions and materials to find the best solution. When a specification calls for a specific polymer, the digital preview of the polymer’s reaction allows them to adjust the mold design and, when needed, the product design. Doing this before initiating the tooling build avoids retooling costs from an unexpected issue.
Preventing Injection Molding Defects
The complexity of injection molding leaves it vulnerable to generating products with defects ranging from minor surface imperfections to those that impact the part’s structural integrity. Improper tooling design or processing is often the cause. There are several common defects that can occur during plastic injection molding:
- Short shots occur when the mold cavity is not completely filled with plastic material, resulting in incomplete or missing features.
- Air pockets or vacuum voids are bubbles or voids in the part caused by air being trapped in the mold. This happens because either the molding pressure isn’t adequate to force trapped air out or gate placement has resulted in uneven cooling, which causes the material to pull away and create a void.
- Flow lines occur when the injection speed is too slow or there are differences in wall thicknesses, causing the plastic material to cool at different rates, which creates wavy patterns or streaks on the part surface.
- Warping happens when the shrinkage occurs at different rates within the part, causing it to deform or twist. Differences in wall thickness is one reason for warping.
These defects can compromise the plastic parts’ appearance, functionality, and durability, leading to customer dissatisfaction, product recalls, or even safety hazards. Therefore, it is essential to avoid or minimize these defects by optimizing the plastic injection molding process. Mold-flow simulation software can help to optimize the mold and part to prevent defects.
How Simulation Software Helps Us Build Better Products
Our engineers use mold flow simulation during the analysis phase of a project. Once the mold design is input, the software evaluates it and creates color maps of the various properties of the mold flow, including injection pressure, fill pattern, air bubbles, heating, and cooling. The color maps give us a visual of how the mold and resin perform and allow us to see how changing the design will impact the part’s quality.
Moldflow analysis can help our engineers to:
- Analyze the resin flow behavior in the mold cavity and identify potential filling problems, such as short shots, air traps, weld lines, and jetting.
- Evaluate the cooling performance of the mold and optimize the cooling channel layout and size to prevent warping and sink marks.
- Predict the shrinkage and warpage of the plastic part and adjust the mold dimensions and shape to compensate for them.
- Compare different material grades and select the most suitable one for the part design and performance requirements.
- Optimize the gate and runner system to reduce pressure loss, shear stress, material waste, and injection time.
The data provided allows us to adjust the mold accordingly and retest the model. We can test all the what-if scenarios without the cost of building a new mold. The process is continued until the mold is optimized, mitigating risk before production begins.
Moldflow simulation software helps our engineers improve the quality and efficiency of plastic injection molding by providing insights and solutions before making costly physical prototypes or molds. It can also help to reduce trial-and-error testing, rework, scrap, and downtime. Using Moldflow simulation software allows us to create better plastic injection molded parts that meet customer expectations and specifications while saving them considerable money and time.